The different production methods
There are a range of manufacturing techniques for all our product families. Manufacturing plastic parts is a complex process and depends on numerous factors, in particular the properties of the material and the list of requirements for the part’s application
Our means of production of plastic parts
The production method is sometimes determined in advance by the customer’s specification. In the absence of the latter, our industry experts will take charge of determining the most suitable production method for your specification with you.
We use various production methods, but injection moulding is our core business.
Injection moulding is the most widely used process at Bülte for standard plastic parts, above all plastic injection moulding of spacers and plastic injection moulding of washers, which are Bülte’s two flagship product families.
These production methods include:
Plastic injection moulding, forming, milling or turning, traditional cutting, water jet cutting, overmoulding, dip moulding and extrusion.
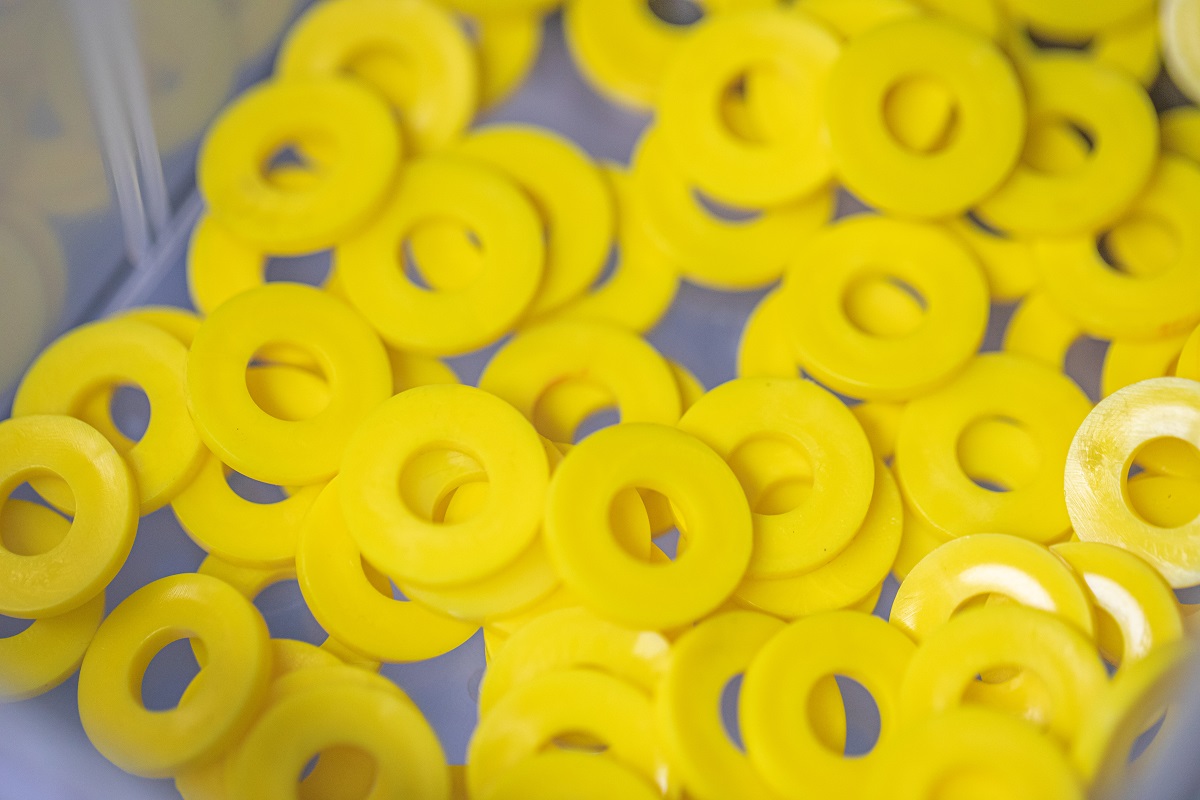
Plastic injection moulding
Plastic injection moulding consists of producing objects/parts from molten plastic material injected under pressure into a mould mounted in an injection moulding machine. We use this process for the vast majority of injection moulded components at Bülte.
When to use plastic injection moulding ?
Plastic injection moulding is a production method designed for manufacturing medium-sized or large batches of identical parts.
It generally starts to have an advantage over other methods from a few hundred parts. It is also the most widely used process in the plastics industry.
The most suitable polymers for injection moulding
In plastic injection moulding, we use materials that can be formed using heat. This is thermoplastic material. This property makes them easily pliable, adaptable to the mould and almost endlessly recyclable. It is for this reason that we regrind the surplus raw material, which falls from the mould, i.e. the sprue, when the part is ejected.
The process is actually based on the mould design, which is precisely tailored to the shape of the parts required.
Forming
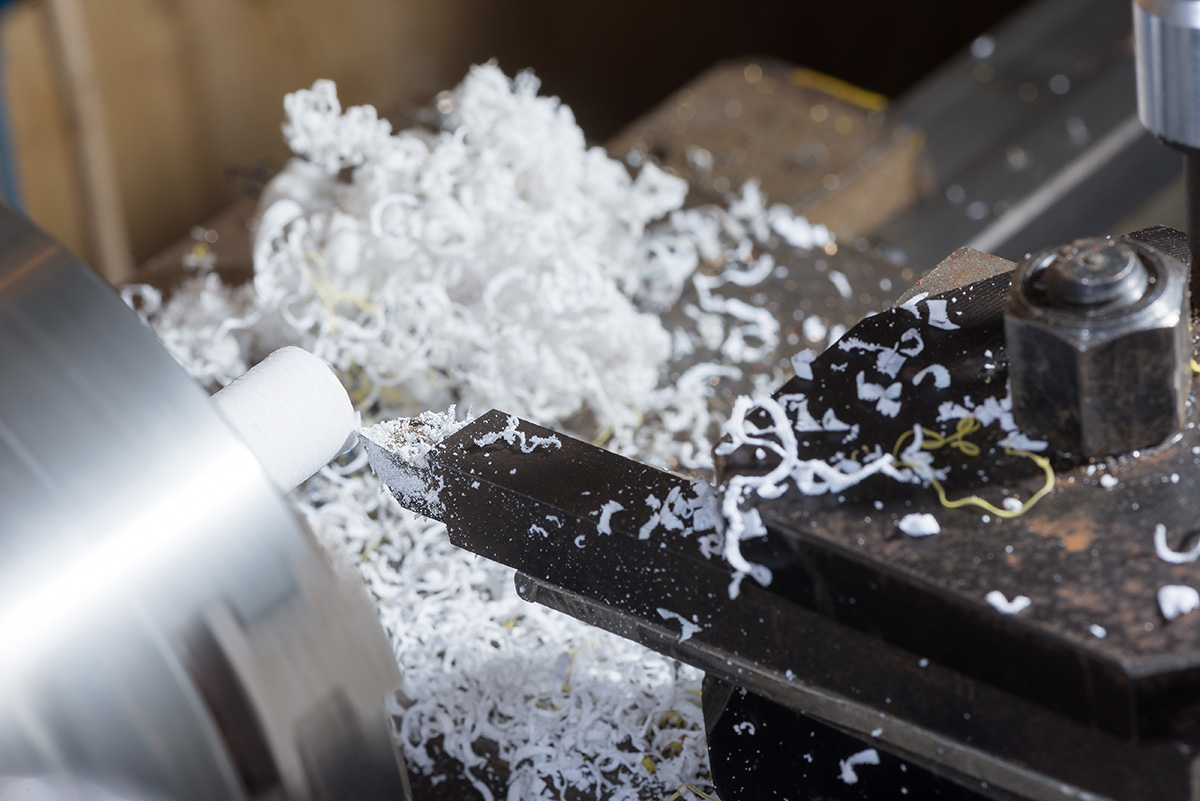
Plastic forming is a suitable method for producing small and medium-sized batches of technical components.
Forming is used to shape parts using conventional wood and metalworking tools and machines, there is, therefore, no need to invest in complex and expensive tooling. What's more, the ability to produce parts with thin and variable wall thicknesses with tight tolerances is a real plus.
In addition, producing parts by forming enables complex assemblies of different components to be designed in different materials, which are often unattainable and frequently incompatible in the case of injection moulding, such as the combination of thermoplastics with thermosetting plastics. Certain materials, such as PTFE-based materials and mixtures of polyamides, are very difficult to injection mould. It is a reliable and stable production method, which allows a certain degree of freedom in terms of design.
Turning
As a technique, turning refers to a sphere of manufacturing where parts, such as screws, bolts, spindles, etc. are machined by removing material from a plastic rod, using a cutting tool (generally a knife tool).
Turning is performed on machines known as “autolathes” or “automatic lathes”, the movements of which are generated by cam or numerical control (CNC) systems.
The parts are turned in small, medium-sized and large batches using conventional automatic lathes (with a blade) or CNC lathes. They are turned in succession in the rod, with the aim being to achieve a high level of productivity and precision.
This method is primarily used for the automotive, aviation, aerospace, medical, electronics, household appliances, connector technology, building, agricultural machinery and armaments sectors, as well as the electricity and nuclear industries.
Traditional cutting
This method consists of cutting thermoplastic sheets of different sizes and thicknesses using either laser or CNC machines.
This production method provides complete freedom in terms of shape and unique precision in terms of execution.
For unit or mass production, we cut all your projects. This technique produces a very clean finish.
Water jet cutting
This technique is a manufacturing process, which consists of cutting the material using a very high pressure jet of water, to which a very fine sand is added, if necessary. Water jet cutting is reliable, precise and environmentally-friendly.
There are many advantages of water jet cutting :
- the high cutting speed
- the ability to cut materials into different shapes
- flexibility (from prototyping to mass production)
- the ability to cut large thicknesses
However, the main advantage is the cold cutting process, which does not trigger any changes in the structure of the material.
Overmoulding
Overmoulding is a technique, which consists of moulding an already finished product. At Bülte, we use the overmoulding technique for plasto-metallic nuts and screws, i.e. bi-material parts. This method consists of injecting plastic over a metal insert: in this instance, Bülte uses overmoulding with stainless steel, brass, aluminium and titanium.
Dip moulding
What is dip moulding ?
The PVC dipping method is an economical way of manufacturing protective covers in soft PVC.
This manufacturing technique has multiple advantages: a wide range of dimensions, low tooling costs, standard or custom parts possible from small and medium series.
Dipping, as its name indicates, consists in dipping a mandrel in a plastic bath.
After passing through the material bath, we obtain a part with the same internal shape as that of the mandrel.
Surface finishes
The surface finish of a plastic part quite simply means the part’s aesthetic appearance. It is the part's finish. The choice of surface finish must be made when the mould or tool is designed.
There are various tooling finish textures for creating the surface finish of a plastic part. The textures can be smooth, slightly rough, very rough, glossy, matt, etc. The texture of plastic parts is created directly in the plastic injection moulding mould.
The surface of injection moulded parts is textured or polished.
Depending on the product family at Bülte, we generally use smooth polishing for washers, screws, nuts, spacers and bushings, i.e. all injection moulded parts where finishing is the least costly insofar as it corresponds to a raw surface, which may exhibit injector marks on the moulded parts.